What is a tachogenerator?
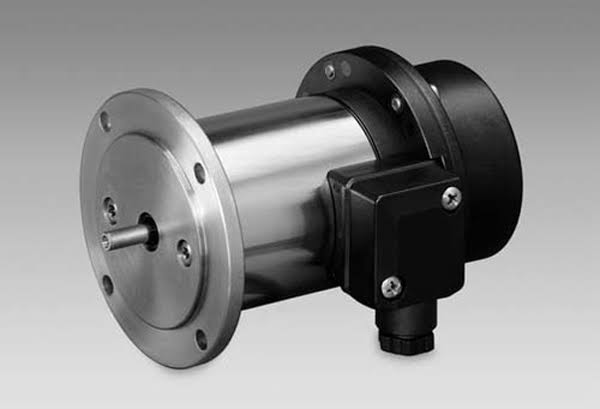
Tachogenerators are essential for many industrial and technological applications because they are electromechanical devices that convert rotating speed into a proportionate voltage output. These transducers have developed from basic speed measurement tools to complex devices that allow precise control and monitoring across various sectors by utilizing the principles of electromagnetic induction.
In the past, the growing need for precise rotational speed measurement in the emerging field of electrical engineering led to the development of tachogenerators. Although practical, early designs were less long-lasting because they frequently relied on brushing mechanisms prone to wear and tear. However, tacho generators experienced a dramatic change due to developing sophisticated materials, improved electromagnetic principles, and advanced production techniques.
Today’s industrial environment requires tachogenerators, which are now essential. They are the cornerstone of feedback control systems, guaranteeing peak motor performance, facilitating smooth automation, and preventing catastrophic failures of vital equipment. To maximize energy production and improve grid stability, the power generating industry, in particular, significantly depends on tachogenerators to monitor and control the rotational speed of turbines and generators.
Furthermore, tachogenerators have an impact outside of the industrial sphere. They are essential parts of robotics, scientific research, and automobile safety systems, among other fields.
How Tachogenerators Work: Unveiling the Mechanics of Speed-to-Voltage Conversion
The basic idea underlying the functioning of a tachogenerator is Faraday’s Law of Electromagnetic Induction. According to this law, a conductor experiences an electromotive force (EMF) when the magnetic field changes. A voltage proportional to the rotation speed of a conductor rotating in a magnetic field is produced in the context of a tachogenerator.
Internal Components and their Interplay
- Rotor: The rotor, typically a cylindrical assembly of ferromagnetic material, is the rotating component of the tachogenerator. It is designed to cut through the magnetic field lines of the stator, inducing an EMF within its windings.
- Stator: The stationary component’s stator houses the permanent magnets or field windings that create the magnetic field within which the rotor rotates. The configuration of the stator magnets or windings determines the type of tachogenerator (AC or DC) and its output characteristics.
- Windings: Encircling the rotor or stator are coils of insulated wire. The windings are usually on a DC tachogenerator’s rotor and an AC tachogenerator’s stator. The induced EMF is captured by the windings and sent as an electrical signal.
- Magnets: Permanent magnets or electromagnets within the stator create the magnetic field necessary for induction. In some designs, the magnets are placed on the rotor, and the stator windings modulate the magnetic field strength.
Generating Voltage: The Transformation Procedure
The magnetic flux connected to the rotor windings fluctuates constantly while the rotor rotates inside the stator’s magnetic field. This shift in flux causes the windings to experience an EMF, as Faraday’s Law requires. The induced EMF’s magnitude is directly correlated with the flux’s rate of change, which is associated with rotation speed. This proportionality makes applications involving feedback control and precise speed measurement possible.
Types of Tachogenerators: Exploring AC and DC Variants
Based on the characteristics of their output signal, tachogenerators can be divided into two types: direct current (DC) and alternating current (AC). Different types are appropriate for various industrial and technological circumstances due to their unique features, benefits, and uses.
AC Tachogenerators: Harnessing the Power of Alternating Currents
Using the electromagnetic induction principle, AC tachogenerators produce an alternating voltage signal whose frequency is proportional to the rotating speed. They usually comprise a stator with several windings and a permanent magnet rotor. A sinusoidal voltage waveform is created when the spinning rotor induces alternating currents in the stator windings.
- Working Principle: Each stator winding experiences an alternating current due to the multi-pole permanent magnet rotor’s rotation. Because these currents’ frequency is precisely correlated with rotational speed, AC tachogenerators are perfect for high-speed uses.
- Construction Details: Since AC tachogenerators often don’t require brushes or commutators, they are brushless. Three-phase arrangements of the stator windings generally result in a smoother output waveform and improved efficiency compared to single-phase solutions.
- Advantages:
- High accuracy and sensitivity, especially at higher speeds.
- The brushless design ensures longevity and reduces maintenance requirements.
- Excellent linearity over a wide speed range.
- Disadvantages:
- The output signal may contain ripple or noise.
- It may require additional signal conditioning for specific applications.
- Common Applications:
- High-speed motor control and feedback systems.
- Precision speed measurement in robotics and automation.
- Turbine and generator monitoring in power generation.
DC Tachogenerators: Simplicity and Robustness
DC tachogenerators produce a direct current voltage signal, and its magnitude is related to rotational speed. Usually, they consist of a stationary permanent magnet field and a spinning armature with windings. A DC output is produced by commutating the voltage the magnetic field induces in the windings as the armature rotates.
Working Principle: A voltage is induced in the armature windings by rotating the armature within the permanent magnet field. *The voltage is subsequently changed to DC using brushes and a commutator.
Construction Details: Brushless and brushed DC tachogenerators are offered. Brushless designs use electrical commutation for increased longevity and dependability, while brushed variants use mechanical brushes to transfer electricity from the revolving armature.
- Advantages:
- Simple and robust construction.
- Cost-effective compared to AC tachogenerators.
- Suitable for low-speed applications.
- Disadvantages:
- It may exhibit limited accuracy and linearity at low speeds.
- Brushed types require regular maintenance due to wear and tear.
- Common Applications:
- Low-speed motor control and feedback systems.
- Industrial process control and monitoring.
- Speed measurement in conveyor belts and other material handling equipment.
- Engineers and technicians can choose the best technology for their particular applications by being aware of the subtle differences between AC and DC tachogenerators.
Applications of Tachogenerators: Pervasive Across Industries and Technologies
Because of their adaptability and dependability, tachogenerators are necessary for various applications spanning several sectors and technological disciplines. Numerous vital operations rely on their precise measurement and management of rotational speed, which guarantees top efficiency, safety, and performance.
Industrial Applications: The Backbone of Modern Manufacturing
- Motor Speed Control and Feedback Systems: Real-time feedback on motor speed is provided by tachogenerators, which are essential components of closed-loop motor control systems. This information is necessary for maintaining precise speed regulation in applications where consistent and exact motion is critical, such as robots, CNC machining, and conveyor systems.
- Power Generation and Monitoring: In power plants, tachogenerators monitor the turbine and generator rotational speeds to ensure they operate within safe and effective limits. This real-time monitoring makes Proactive maintenance possible, which also reduces costly downtime.
- Process Control and Optimization: Tachogenerators play a crucial role in several industrial processes, including the production of textiles, steel, and paper. They enable precise control over process parameters, resulting in enhanced product quality, decreased waste, and better resource use by precisely measuring the speed of spinning machinery.
Beyond Industry: Expanding Horizons
- Vehicle and Transportation System Speed Measurement: Wheel, engine RPM, and transmission speed are all measured by tachogenerators in automotive and transportation applications. This data depends on Anti-lock braking systems (ABS), traction control, and other safety measures.
- Motion Control Systems and Robotics: Tachogenerators are crucial for accurate motion control in automation and robotics. They make robots indispensable in manufacturing, assembly, and material handling operations by enabling them to perform complex actions precisely and repeatedly.
- Scientific Research and Instrumentation: Centrifuges, spectrometers, telescopes, and other scientific instruments are among the devices that employ thermogenerators. Their great degree of precision in measuring rotational speed helps various study domains gather and analyze data with accuracy.
The pervasive use of tachogenerators underscores their significance in modern technology. As industries evolve and new applications emerge, the demand for reliable and accurate speed measurement and control solutions will only intensify.
Advantages and Disadvantages of Tachogenerators: Balancing Precision and Practicality
Although they are quite useful in many applications, tachogenerators have advantages and disadvantages of their own. Engineers and technicians must know these trade-offs to choose the best speed-sensing technology for a particular application.
Advantages
- Robust and Simple: Tachogenerators boast a straightforward and durable construction, translating to reliable performance in demanding industrial conditions with exposure to dust, vibrations, and temperature variations.
- Cost-Effective: Compared to encoders or resolvers, tachogenerators are generally more economical, making them attractive for budget-conscious projects where extreme precision isn’t paramount.
- Harsh Environment Resilience: Their robust build and lack of delicate electronics (in brushless types) enable them to withstand vibration, mechanical shock, and temperature extremes, making them ideal for challenging industrial settings.
Disadvantages
- Limited Accuracy: While accurate enough for many applications, tachogenerators may need to match the precision of encoders, particularly at lower speeds. With their digital output, encoders offer more granular speed data, which is crucial for some high-precision applications.
- Maintenance (Brushed Types): Brushed DC tachogenerators require periodic maintenance due to brush and commutator wear. This leads to downtime and costs, though brushless designs alleviate this concern.
- Susceptibility to EMI: Tachogenerators can be affected by electromagnetic interference from nearby equipment or power lines. This interference introduces noise and errors in the output signal, potentially impacting speed measurement accuracy.
By carefully assessing application requirements, engineers can leverage the strengths of tachogenerators while mitigating their weaknesses, ensuring optimal performance and reliability.
Tachogenerators remain indispensable in various industrial and technological applications due to their unique blend of simplicity, robustness, and cost-effectiveness. While they may not always match the precision of cutting-edge technologies like Baumer Encoders, their resilience and versatility make them valuable assets for engineers across diverse fields.
The particular needs of the application ultimately determine which speed sensing technology—tachogenerators or Baumer Encoders—is best. Engineers may choose the ideal solution that balances performance, dependability, and cost-efficiency by carefully weighing variables, including accuracy, cost, maintenance requirements, and environmental conditions.