Plugging The Leaks: Preventing And Fixing Concrete Pumps Leakage
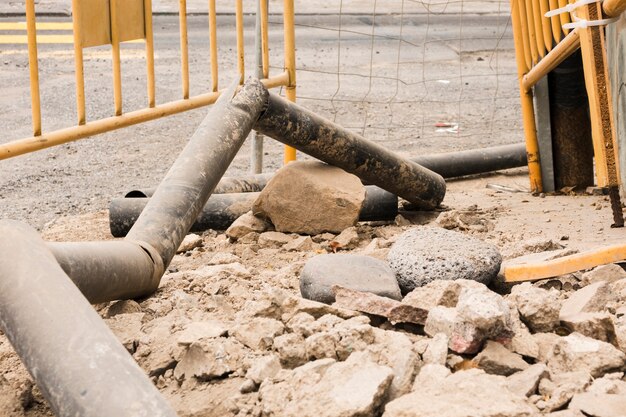
You’re pumping concrete to pour a new driveway when you notice drips splattering below the boom line. Looks like you’ve sprung a leak. As per experts like CGS Equipment, while tiny drips may seem harmless, leakage while concrete pumping can lead to major headaches down the line if neglected. Let’s take a proactive look at decisively defeating leakage.
In this article, we’ll explore common causes of concrete pumps leaks and key maintenance strategies to stop leaks in their tracks. Consider this your game plan for leak prevention and damage control when pumping concrete. Let’s keep things sealed up tight.
Worn Out Seals and Packings
Repeated pumping wears down pump seals and packing rings, eventually causing drips and leaks. Routinely replacing worn seals and packing before they fail prevents leakage. Don’t wait for visible drips – be proactive with replacements based on usage hours. Good maintenance defeats leaks.
Clogged delivery line
High pump pressure from clogged lines strains system seals, blowing out gaskets and packings. Keeping lines clear prevents buildup of concrete and debris that increases pressure and leakage risk. Routinely flush lines thoroughly between uses and check for obstructions. Clogs multiply pressure exponentially.
Improper Lubrication
Moving pump parts need proper oiling and greasing to stay leak free. Insufficient lubrication causes higher friction, heat, and wear. Sticking or binding parts then fail. Closely follow manufacturer lubrication guidelines. Don’t take shortcuts – proper lubrication makes pumps run smoothly.
Misaligned Components
The pumping system contains many interconnected and moving parts. Misalignment puts abnormal stress on components, causing distortions and cracks allowing leaks. Qualified technicians should routinely check and correct any misaligned parts for leak prevention. Keep everything aligned and turning true.
Overheating Issues
Excessive heat dries out seals and gaskets, causing shrinkage cracks that lead to leaks. Ensure pumps don’t overheat through proper operation, lubrication, and ventilation. Monitor for overheating and shut down pumps when necessary to allow cooling. Heat control prevents cracked seals.
Excessive Vibration
Too much pump vibration from worn parts or mounting issues can worsen leaks or shake apart sealed components. Isolate pumps from vibration with dampeners. Excess vibration accelerates wear everywhere. Smooth operation prevents leakage. Fix mounting and alignment problems first.
Using Wrong Seals
Seals have precise design and material specifications. Using inferior or incorrect seals inevitably causes early leakage failures. Don’t cut corners with seals. Consult manuals and get manufacturer advice to identify proper replacement seals and packings. Right seals = no leaks.
Incorrect Pipe Connections
Using mismatched or undersized couplers and clamps leads to unstable connections prone to working loose and leaking over time from pump vibration and pressure. Double check that all pipeline connection pieces match pump ports and rating specs. Tighten clamps fully. No leaks.
Conclusion
By staying proactive with preventative maintenance and operating practices, concrete pumping crews can keep leakage at bay and enjoy smooth pumping. While tiny drips may seem harmless, leakage while concrete pumping can lead to major headaches down the line if neglected. Don’t tolerate bothersome drips – stop concrete pump leaks in their tracks.