Applications of Plastic Injection Molding in the Automotive Industry
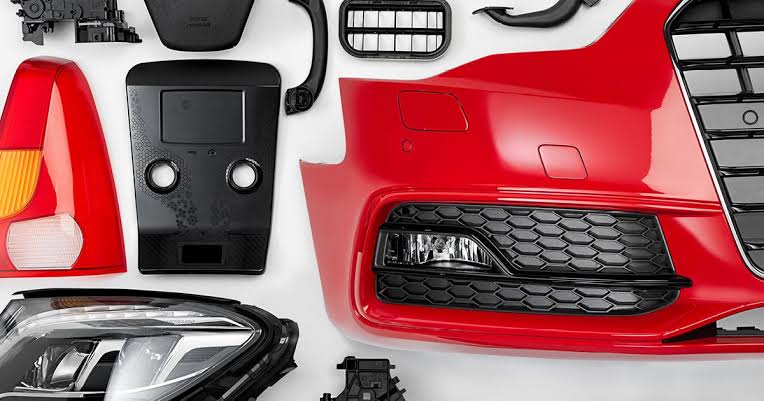
The assembly line might have been one of the biggest inventions in the automotive industry but it has been rivaled by another big manufacturing technique known as plastic injection molding.
Where complex intricate design is concerned, plastic injection molding in automotive construction ensures the precise creation of these automotive components. Frankly, this has revolutionized automotive manufacturing with its numerous benefits including cost-cutting and efficiencies in time, materials, and energy. It also combines design flexibility with durability to meet stringent industry standards for safety and quality.
It’s no gain says that injection molding has shifted many automotive mindsets from impossible to possible giving more options for components that are for dashboard manufacturers and even components under the hood.
so, in this post, we’ll explore the many reasons why the automotive industry has become a landscape of plastic injection molding applications, especially given the cost efficiency and sustainability mandate of the industry. So, if you’re ready, let’s dive in together.
Why Plastic Injection Molding is Ideal for the Automotive Industry
The race for the most cost-efficient and precise manufacturing method has been on from the inception of the automotive industry given the complexity involved in the production process. thankfully innovative techniques like automotive plastic injection molding came in the nick of time. Let’s walk through some of the benefits of this manufacturing method for the automotive industry.
- Precision and Consistency
Where intricate components like connectors and air vents are the order of the day, incurring just the tiniest little bitty error can throw the whole production off. Fortunately, plastic injection molding ensures that every intricate detail is delivered with high precision.
Furthermore, the consistency of this production method is very high considering that it uses cutting-edge technology and advanced machinery to deliver these parts. so, it doesn’t matter if it’s 10 out of 100,000 pieces, it is consistently accurate.
- Cost-Effectiveness
It is easy to assume a high cost given the high level of precision the injection molding brings. but that is a common myth that novices in the industry often peddle. The truth is this: plastic injection molding was built for high-volume manufacturing where it immensely cuts down production costs. In essence, a manufacturing industry like automotive production where components are manufactured in large quantities benefits greatly from plastic injection molding as it not only automates many of the production processes but significantly cuts the cost per unit component. In addition, cost reduction is also gleaned from the removal of human labor and errors that often lead to huge wastage and associated costs.
- Lightweight and Durable Components
With the high cost of gas and the consumer demand for easy driving, the preference for lightweight materials in automotive manufacturing rings ever so loudly.
Thankfully, plastic injection molding service of Kemal helps to achieve all of these lightweight material preferences and benefits without hampering the balance of automobiles. But that’s not all. The durability of these lightweight materials surpasses traditional metal materials by light years keeping automotive components fit for purpose for many years.
- Design Flexibility
With complex designs comes manufacturing difficulty especially with traditional manufacturing methods like metal stamping. but not with injection molding as this is its forte. The flexibility injection molding affords is rarely achieved by other methods given its accommodation of intricate and complex geometries.
This benefit frees up the innovative abilities of design engineers giving them the versatility they need to proffer novel solutions to design problems. Ultimately, the result is both a functional and eye-catching component.
Key Automotive Components Manufactured Using Plastic Injection Molding
Gone are the days when plastic was criticized as unsustainable and cheap. Today it is the bedrock of many manufacturing industries including the automotive sector. And it’s no case of compromise, but one of innovative excellence enabling new possibilities, especially in the manufacture of durable and efficient components. Let’s take a closer look at some of these automotive components that this technology has helped to shape.
- Interior Components
A careful look at your car interior will reveal some components that do not meet the quality of traditional materials like wood and metals but often surpass them in quality and durability. components like dashboards, consoles, and panel trims are made from some of the most advanced plastic materials, exuding both luxury and premium finishes. Additionally, they outlive their traditional counterparts with their resistance to wear and tear.
- Exterior Components
Interior components are not the only suitable application of plastic injection molding. Thankfully, innovative plastic materials have been developed over the years to handle both the rigidity and weather-resistant requirements for external automotive parts.
A closer look at bumpers, fenders, and grilles reveals some of the strongest materials that withstand high impacts and external forces. These components have been made from sturdy materials like reinforced plastics matching and surpassing traditional materials in performance and aesthetics.
- Under-the-Hood Components
Again, plastic products continue to amaze the world with their ability to withstand different forces and harsh conditions including the heat and pressure often associated with under-the-hood components.
For instance, air ducts and fuel systems found under the hood of automobiles generate some of the most insane heat and pressure levels. However, plastic polymers have been specially engineered to withstand these impacts making for some of the most durable under-the-hood components. Their success in this arena of automotive components has made them the darling of many automotive manufacturers.
- Functional Parts
Now, there are automotive components that often seem too small to mention but they act as the backbone of the bigger components that often make the headlines when talking about auto parts. for instance, bumper clips, wiring connectors, and fasteners are rarely mentioned in the grand scheme of things, nevertheless, being made of plastics ensures that they are lightweight and durable, ensuring that the bigger components stay rigid in place. This reliability on the part of these seldom-mentioned auto components goes even further to ensure user comfort and safety in features like seatbelt operations and airbags.
- Lightweight and Safety Parts
Finally, there are the features that ensure that automotive manufacturing meets the stringiest of measures when it comes to safety. As hinted previously, these safety features and mechanisms are mostly powered by injection molded plastics that have some of the highest weight-to-strength ratios. Their lightweight ensures that automotive products as a whole are less bulky and more efficient.
Advantages of Using Plastic Injection Molding in Automotive Manufacturing
Just looking at the sheer number of components that comprise a car can give anyone an idea of the level of detailing and meticulousness that went into its production. Thankfully, cutting-edge manufacturing technologies like plastic injection molding help to achieve this speedily. Below are even more benefits of plastic injection molding to automotive manufacturing.
- Material Variety
When seeking a manufacturing method that has a wide variety of material options to meet your manufacturing needs, plastic injection molding often comes to mind.
It offers materials that meet various requirements including durability, impact resistance, heat resistance, and lightweight making it easy to achieve bespoke production.
For instance, advanced composites, reinforced plastics, and polymers are some of the varieties of materials that plastic injection molding affords automotive manufacturers. These materials also give them the versatility and flexibility they need to innovate.
- Rapid Production and Scalability
The speed of production is yet another critical benefit of employing injection molding automotive manufacturing as all you need is one mold to produce components in high volume. Imagine the dynamic nature of automotive consumer demand and the rapid rate required for manufacturers to adapt. using any other method won’t cut it as it will significantly slow down the manufacturing process. This mass-producing ability and the consistency with which it produces complex geometries is the secret behind assembly lines churning out cars in multitudes.
- Improved Fuel Efficiency
With the rising cost of gas, one of the foremost demands on the list of automotive consumers is efficient cars. Fortunately, automotive plastic injection molding is up to the task with constant churning out of lightweight plastic components which significantly reduces the bulk weight of automobiles.
Consequently, a lightweight car results in a more fuel-efficient one with a plus on environmental sustainability as it reduces its carbon footprint.
- Enhanced Sustainability
With more push for sustainable and environmentally conscious manufacturing the automotive industry is slowly but surely getting on the train of environmentally responsible manufacturers.
Frankly, plastic injection molding has been one of the beacons of hope when it comes to producing environmentally sustainable materials. With the popularity of recyclable plastic and biodegradable plastics increasing, it is only a matter of time before traditional material fades out.
Conclusion
What does all these mean? It means you really can’t talk of modern automotive manufacturing without a mention of plastic injection molding seeing that it has become the backbone of the manufacturing process. Its support for innovative materials, precision for intricate components, and versatility endear it even more to automotive designers and manufacturers.
There is no doubt that plastic injection molding has contributed immensely to the revolutionizing of automotive manufacturing contributing manufacturing materials with critical parameters. These factors include high impact resistance, weight reduction, and pressure resistance making it a versatile and innovative manufacturing process.
Ultimately, the end of these favorable combinations which include sleek, highly functional, and fuel-efficient automobiles is not in sight yet. It is expected that the plastic injection molding industry will continue to adapt to the demands of automotive consumers in the coming years. So, if you’re like us you want to keep a keen eye out for what the future holds.